Table of Contents
Introduction
Logistics is a crucial part of Wal-Mart’s business because of the high quantity of resources its logistics requires that is an impact of the high quantity of products it is managing. Wal-Mart has constantly improved its logistics performance the previous years and now strives to increase its competitiveness and performance even further (Jacobs and Chase, 2014). To achieve this, Wal-Mart wants to identify potential areas of improvement by enhancing its understanding of how it is managing its logistics performance. This is the reason the company internally and externally evaluates its logistics performance measurements to enhance its competitiveness.
The function of logistics in business has increased both in strategic importance and scope over the previous ten years. Logistics is a chain of complex actives that require a set of metrics to measure the performance. Today, logistics is influencing lots of core business processes like alliance/partnership building, product design, and customer selection. Getting a solution of how to successfully management logistics could be a struggle for organizations since there is no best practice because organizations act differently in different industries and in different contexts (Russell, Swanson, and Blinge, 2015). Due to the context effect, it is significant for organizations to put into consideration of their critical success factors and specific conditions when developing their logistics strategy rather than adapting a solution suitable for somebody else.
What are Wal-Mart Logistic Performance Measurements?
Unmeasured performance goes uncontrolled and consequently becomes unmanageable. Performance measures play a vital role in the management of Wal-Mart and are of significance to logistics managers. Performance measurement is considered as an avenue for Wal-Mart logistics managers to create sustainable competitive advantage by providing reliable and timely indications of both shortcomings and performance successes (Russell, Swanson, and Blinge, 2015). Performance measurement is an important competency in the company’s achievement of outstanding performance. Just like Wal-Mart, retail organizations are faced with managing increasingly competitive and complex operations; they must constantly evaluate the existing metrics or even develop new ones.
Logistic performance is a multi-dimensional and is identified as a degree of differentiation, effectiveness, and efficiency associated with the achievement of activities. Jacobs and Chase (2014) identified that logistics performance is a multidimensional function of effectiveness, efficiency, and differentiation, and all are pursued simultaneously. Efficiency is one of the important operational measurement areas that is applied in the measuring processes and is used at multiple levels from particular processes measuring performance of the whole supply chains. Efficiency is the measure of how economically the company’s resources are used (the ratio of resources used against the derived result). Effectiveness refers to the extent to which the goals of logistics function are achieved. Many critical areas of effectiveness include product availability, guarantee, convenience, and fulfillment time. Xin, He, Bewli, Bowman, Feng, and Qin (2017) identified that differentiation is another extended definition of efficiency and effectiveness. Differentiation is the capability of Wal-Mart to create value for the customers through the distinctiveness and uniqueness of logistics services. Differentiation involves comparing results of logistics activities to competitors. Logistics performance plays a significant role in achieving the company’s goals. The assessment is based on how well the goals are met and to what level the overall performance and productivity reflect logistics performance. Thus, logistics performance assists the fulfillment of the company’s’ strategy and objectives and satisfying the customers.
What does Wal-Mart use to measure their logistics?
Several organizations like Wal-Mart have been tracking their logistics performance based majorly on financial accounting principles (Kumar, Sunder, and Sharma, 2015). But such measures are biased towards improving the financial position of the company, but are mainly inadequate to measure logistics performance. Such measures lack relationships to vital strategic, non-financial performance. Also they may not be focused towards creating forward looking perspective and do not directly link operational efficiency and effectiveness. Due to these shortcomings, there are many other measurement approaches that organizations use to measure supply chain performance.
Performance measurement offers an approach to identify the potential and success of management strategies, and facilitating understanding of position and progress. This model emphasizes the activities of supply chain as enterprises linked through the business relations. This model emphasizes the integration of business process. A supply chain is the integration of main business processes from consumers through suppliers and others stakeholders. The success of logistics needs a change from managing individual functions to integrating activities within main supply chain business processes (Jacobs and Chase, 2014). The integrated performance measurement model is made to ensure the integration between the external and external performances. Any organization cannot be productive by eliminating either an external or internal performance. Thus, it is critical to have an integrated measurement model which measure both external and internal activities. Be it no cost performance or cost involved, both the external or internal activities are measured with the assistance of this integrated performance measurement model (Ailawadi and Farris, 2017). For instance, measuring the internal performances like new product introduction, delivery time, and project life cycle time results in measuring the external performances like increased customer attrition rate, number of repeated and new customers, and market value of the company.
Supply chain system is inter-connected components of different kinds. Looking at what occurs in the separate but interconnected unit, and optimizes the routines ensures that the system is as efficient and effective as possible and improves the performance of each unit within the system. Wal-Mart uses metrics for performance evaluation of planned order procedures to measure the manner in which the order-related activities are conducted (Ailawadi and Farris, 2017). This measurement also involves vital issues such as path of order transverse, order lead-time, and order-entry method. Besides that, the company also measures supply chain partnership and related metrics. Partnerships in a supply chain (for example, outsourcing) are vital. Several times, such partnership decreases product introduction times. Faster introduction of a product significantly depends on quick responsiveness and reliability of suppliers. This assists to measure the level of competitiveness.
Also, Wal-Mart uses the production level measures and metrics that majorly evaluate production processes (i.e. product quality, cost, speed of delivery, and on the delivery flexibility and reliability). Waller, Fawcett, and Johnson (2015) viewed that the performance evaluation of delivery link is another metric that the company uses to evaluate supply chain performance. This directly deals with the customer delivery of products and services. Sometimes, it is identified as the driver of customer satisfaction. However, delivery operations are quite dynamic, thus make the evaluation and consequent improvement strategy of distribution system difficult. Also, the company measures customer satisfaction and service to evaluate supply chain performance (Ailawadi and Farris, 2017). With advanced global markets and increased globalization, efficient supply chain metrics and performance measurement must be linked to customer satisfaction. Such measurement is required to integrate customer specification in the control of the process.
We can do it today.
The HPMS (hierarchical performance measurement system) model links different analytical model levels into an integrated (blended) one. Through the hierarchical performance measurement system model, companies can measure the performance of every function as well as its sub functions aligned with the overall organizational objectives. When the HPMS model is used to measure every function in a department level, this process automatically enables the system to evaluate program level activities (Kumar, Sunder, and Sharma, 2015). When the company has the system implemented to measure and monitor the performance of all main functions and sub-functions, achieving company goals becomes feasible. The HPMS model is frequently utilized in measuring supply chain performance. Areas utilized as main logistics in the HPMS model include finance, quality control and assurance, sub-functional and overall productivity, customer satisfaction through service, and asset management.
Organizations also use balanced scorecard model to measure the performance of all levels of activities towards achieving organizational goals. Such activities are measured based on customer, financial, internal project, and innovation and learning perspectives. Frustum or low level system model is also relevant in performance measurement. In this model, performance measurement concentrates on the low level operations, and not the top level (Waller, Fawcett, and Johnson, 2015). This model measures the performance of people, activities, and the functions at the lower levels. This model assists to measure economic financial performance and build lower level activities into KPIs (key performance indicators).
Who or What do they compare their performance too?
Nowadays, consumers are becoming more price-conscious and more demands and this compel retailers to develop a more responsible supply chain simultaneously as keeping the costs as low as possible. Thus the logistics performance is becoming increasingly vital for a retail company which wants to be successful by responding to the demands of consumers. Xin, He, Bewli, Bowman, Feng, and Qin (2017) opined that measuring performance internally within the organization is frequently used though it can also be important to conduct as external comparison like a benchmarking. By conducting a benchmarking, it is possible to get ideas from other organizations and adapt them to build competitive advantage.
One retail company which works to improve its logistic performance is Wal-Mart. Wal-Mart has constantly improved its logistics performance during the past years and strives to improve its competiveness and performance even further. Wal-Mart strives to identify potential areas of improvement by improving its understanding and how good its logistic performance is compared to other retail companies. Conducting benchmarking exercise has helped Wal-Mart to know its logistics performance measurements compared to other retail competitors (Kumar, Sunder, and Sharma, 2015). Benchmarking is a systematic approach where a company (such as Wal-Mart) compares and measures itself against other retail companies in the industry so that to discover, understand, and adapt better practices. The purpose of benchmarking is to get a well performing practice so that to borrow and adapt ideas to gain competitive advantage. By understanding the gap between Wal-Mart’s current performance and the retail competitors’ best practice, Wal-Mart can define goals and strategies which have to be attained in the future to close the gap and make the organization competitive.
Waller, Fawcett, and Johnson (2015) identified that a benchmarking can be used to the practices, services, and products of an organization. It can be used to any area which the company wants to improve and compare against others, and there are various reasons why companies benchmark. Some of the reasons include cutting short the improvement process, to apply it to drive for improvement, and to enhance improvement culture. Some the benefit of conducting benchmarking include to become industry leader, to enhance understanding of the market, to work more proactive, to increase understanding of the competitors, and to increase outcomes produced by the organization and deliver with better performance (Xin, He, Bewli, Bowman, Feng, and Qin, 2017). All the benefits illustrate that make an organization successful and competitive with better understanding of the market. An organization becomes competitive because of benchmarking.
A retail company like Wal-Mart can apply benchmarking to achieve a long-term success by understanding more than internal performance and consequently gain knowledge which enables the organization to improve. This is a form of external benchmarking as the organization seeks external organizations to benchmark towards (Russell, Swanson, and Blinge, 2015). Also there is internal benchmarking in which a company conducts a benchmarking within the organization to obtain the best in-house practices and share the insights of such practices to other departments of the company. External benchmarking is regarded to generate the best advantage since without it; the organization may lack understanding of what a competitive performance is.
KPIs like inventory levels, total logistics costs, and stock damages or loss provide an organization with a snapshot of the logistics performance. KPIs associated with inventory are commonly used in benchmarking. Kumar, Sunder, and Sharma (2015) said that the KPI inventory turnover is vital because it is linked to the logistics performance. Inventory turnover is vital to benchmark because it is the key KPI for measuring supply chain efficiency. Having a high inventory turnover is always bad because it can affect the organization by displaying empty store shelves.
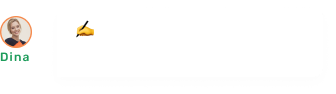
The KPI logistics costs enable organizations to measure their efficiency of supply chain and logistics management operations. By adding all costs associated with logistics a retail company like Wal-Mart can evaluate its performance by benchmarking itself against related companies in the industry with similar logistic processes. Waller, Fawcett, and Johnson (2015) identified that by comparing logistics costs and inventory turnover, the organization can become competitive because by applying corporate measurements of supply chain and logistics management KPIs, the organization increases the level of improvements. A good example is a reduction of 16% of shipment delay accomplished by organizations which benchmark constantly compared to 8% accomplished by organizations not applying benchmarking as an instrument for improving themselves. Irrespective of what KPIs an organization selects to benchmark, it is vital to have a comprehensive action plan to influence stakeholders to support the organization’s competitive supply chain and logistics management strategy and to secure the essential involvement when implementing it.
- Ailawadi, K & Farris, P. (2017). Managing multi- and Omni-channel distribution: metrics and research directions. Journal of retailing, 93(1), 120-135.
- Jacobs, F & Chase, R. (2014). Operations and supply chain management. New York: McGraw-Hill Irwin.
- Kumar, V., Sunder, S & Sharma, A. (2015). Leveraging distribution to maximize firm performance in emerging markets. Journal of retailing, 91(4), 627-643.
- Russell, D., Swanson, D & Blinge, M. (2015). Sustainable logistics and supply chain management: a holistic view through the lens of the wicked problem. World review of international transportation research, 7(1), 21-34.
- Waller, M., Fawcett, S & Johnson, J. (2015). The luxury paradox: how systems thinking and supply chain collaboration can bring sustainability into mainstream practice. Journal of business logistics, 36(4), 303-305.
- Xin, L., He, L., Bewli, J., Bowman, J., Feng, H & Qin, Z. (2017). On the performance of tailored based-surge policies: theory and application at walmart.com. Paper statistics, 2(1), 23-38.