Table of Contents
Introduction
Oil refinery includes the industrial approach of processing and refining crude oil to more useful products such as gasoline, kerosene, diesel fuel, liquefied petroleum gas, and other products. Oil has been an imperative resource for centuries and as previously been used to run many industries, automotive, and automobiles across the globe. Generally, oil is heated and changed into gas and passed through distillation chambers to be cooled. The gases condense into liquid after attaining below their boiling points. However, oil refinery is not as simple as explained above and involves numerous processes and extensive capital investment to ensure that all the operations run effectively. The technological advancement over the years has seen an expansion of the oil refinery processes making them more efficient and eliminating some of the challenges and hazards witnessed. For such concerns, this paper will analyze oil refinery process, equipment applied, basic engineering principles, standard operating procedures, potential health hazards, fault detection, and other components relevant to oil refinery. This is imperative, as it will provide the basic principles surrounding oil refinery, their implication on energy efficiency and costs, and some of the strategies that can be applied to improve or replace the traditional methods in place.
Background
The greatest demand from the distillation process is gasoline, although the other products have great value. The greatest demand from the oil refinery is transport industry that requires more than 50% of the gasoline for use in automobiles. However, crude oil contains 30-40% gasoline, and the increased demand requires specialized approaches to convert petroleum fractions into gasoline (Groysman, 2016). This is typically done through cracking the heavy residual products, reforming the products and isomerization. Crude oil ranges in color from yellow to black and may contain asphalt, paraffin, or mixed base. Crude oil is described as light or heavy depending on the API gravity, or sweet or sour depending on the amount of sulfur content. If the crude oil contains a high amount of sulfur (1-5%), then it is called sour crude while those that contain less than 1% sulfur are called sweet crude. Correspondingly, light crude is greater than 30°API while heavy crude is less than 30°API (Groysman, 2016).
Definition of terms
- Cracking. This involves breaking down the large molecules into smaller potions and heating the residual at high temperatures (AFPM, 2017).
- Reforming. This involves changing the low-quality gasoline molecules to usable materials (AFPM, 2017).
- Isomerization. This involves rearranging the atoms of the hydrocarbon so that the product has the same chemical formula but has a different structure, such as the conversion of butane to isobutane (AFPM, 2017).
- Hydrotreating- involves the removal of impurities from hydrogen to bind with nitrogen and sulfur (AFPM, 2017).
- Desulfurization. This involves the removal of sulfur molecules from the refined oil (AFPM, 2017).
- Coke unit. This processes vacuum resid that is heated to over 900°F and put in coke drums. The resid undergoes thermos cracking and decomposes under the extreme heat. The products from this method include turbine and diesel fuel, naphtha, butane and lighter material, fuel grade petroleum coke, and gas oil for Cat Cracking (AFPM, 2017).
- Alkylation Unit. This unit applies the acid catalyst to combine small molecules collectively called alkylate. Alkylate has a high level of octane and is the cleanest burning fuel among the gasoline blend stocks (AFPM, 2017).
- Reformer Unit. The reformer changes the molecular structure of crude and coker naphthas using heat, moderate pressure and catalysts. This produces a primary blendstock gasoline that is called reformate (AFPM, 2017).
Stages of Refining Oil
Three operations are performed to separate the crude oil into its individual components.
Separation/topping
This is the first step, and the molecules are separated through atmospheric distillation at the normal atmospheric pressure. The oil is heated at a temperature of 350-400°C at the bottom of a 60-meter distillation chamber, causing the oil to vaporize. The vapor rises in the distillation chamber while the heavier molecules remain at the bottom. These materials are mostly residual materials such as bitumen (Planete Energies, 2015). The different molecules condense into liquids at different temperatures in the column, and only the gasses reach the top, where the temperatures have dropped to 150°C. The columns have different trays that collect the liquid at different temperatures. Each tray collects different fractions, typically known as petroleum cut, with the gasses at the top and highly viscous hydrocarbons such as asphalt (bitumen) at the bottom. The heavy residuals are left at the bottom of the distillation chamber and contain many products of medium density. The residual is transferred to another column whereby they undergo another distillation process to recover the medium density products such as diesel and heavy fuel (Planete Energies, 2015).
Conversion
The heavy hydrocarbons that are left in the separation stage are transferred to the stage whereby they are cracked into two or more lighter ones. The conversion process is done at 500°C and is referred as catalytic cracking since it applies a catalyst to speed up the chemical reaction. This process converts 75% of the heavy products into diesel, gasoline, and gas. However, the yield of this process can be improved through adding hydrogen, a process called hydrocracking or using deep conversion to remove carbon. However, Petroleum UK (2017) suggests that it is imperative to consider the cost of the conversion method that is applied. The use of the complex operations such as deep conversion and hydrocarbon increases the cost of the project as well as the use of energy. As such, the refinery has to find a balance between the yield and cost conversion through a cost-benefit analysis to ensure efficiency (Petroleum UK, 2017).
Treating
This approach involves the removal of molecules and substances that are corrosive and that cause increased air pollution, such as sulfur. There are different bodies across the globe that govern the amount of sulfur contained in the refined oil. For instance, the European Union sulfur emission standards are very stringent on the amount of sulfur contained in the oil. Gasoline and diesel sold in the European markets should not contain more than 10 milligrams per kilogram or 10 prats per million (ppm) of sulfur (World Crude Oil Refineries, n.d). The aim of such measures is to reduce the global pollution levels as well as improving the effectiveness of the various catalyst converters that are applied to treat the exhaust gas. For instance, desulfurization of diesel is done at a pressure of 60 bar and temperatures of 370°C. Hydrogen is also applied in the process to remove the sulfur, forming hydrogen sulfide (H2S), which is eventually treated to remove the sulfur (World Crude Oil Refineries, n.d). Kerosene, propane, and butane are removed through a process called sweetening whereby they are washed in a sodium hydroxide (caustic soda).
The treatment of the automotive fuel must also be done to improve the octane rating, which is used to measure the resistance of the fuel to deterioration, on a scale of 0-100. The use of poor quality fuel can lead to engine knocking due to spontaneous ignition of the internal combustion of the engine (Petroleum UK, 2017). If the octane level is too low, the automotive engine may be irreversibly damaged. Therefore, there is a need to improve the octane rating to between 95 or 98. This process is called catalytic reforming and uses platinum as a catalyst at a pressure of 60 bar and temperatures of 500°C. This approach converts the saturated cyclic/naphthenic hydrocarbons into unsaturated cyclic/aromatic hydrocarbons that have a higher-octane rating. Other chemical reactions such as alkylation can also improve the octane rating (Petroleum UK, 2017).
Methods
Fault Detection
There are several challenges that face the oil refinery industry since it deals with complex methods and systems. The timeliness, effectiveness, and accuracy of the fault detection and diagnosis will increase safety, product quality, and reduce the downtime and costs of operations. Most of the oil refineries rely on the skill and experience of the employee in the detection and solving some of the faults. However, automatic sensors are highly recommended in the view of the complexity of the industry as well as the heavy workload among the employees (Freyermuth & Isermann, 2014). However, there are several challenges in developing and implementing the automated fault detection devices. One of the limitations is the poor capability of the analysis tools or algorithms since there are numerous sources of errors within the field, thus making the construction of a single error-detecting system difficult. The other challenge is the intuitive approach of the operators as they may not utilize the automate fault-detection machines. The other challenge is the cost implication of purchasing, maintaining, and running the new technology. Some employees may also be over-reliant on the machines which can malfunction at any moment, thus posing a grieve danger to the staff (Freyermuth & Isermann, 2014).
It is crucial to adopt a fault detection device that will monitor the variables and interpreting the variations accurately in any chemical plant. One of the fault detection technologies that can be adopted is the wavelet analysis (Marti et al., 2015). This approach is crucial as it reveals various frequencies of different variables that can be applied in detection of faults in petroleum industries. The continuous wavelet transforms the results and show discontinuities in the location of a fault and can indicate them better than any seismic investigation (Marti et al., 2015).
Standard Operating Procedures
The oil refinery method can be divided into two parts, which are upstream and downstream. The upstream activities involve the exploration, production, while the downstream activities involve refining and marketing the products (Koodali, Golisz, & Armstrong, 2017). There is also the green side of the operations that are tasked with evaluating and complying with the environmental regulations in place. The chemical engineers are continuously involved in the determination of the best approaches to reduce the negative environmental impact of petroleum products (Koodali et al., 2017). The typical duties involve developing efficient and better approaches of turning crude oil into various components such as automotive and aviation fuel. Correspondingly, they should continuously monitor the quality and improve the yield at the existing sites through the application of modern and cost-effective methods (Koodali et al., 2017).
Health Hazards in Oil Refinery
Like many similar industries, oil refinery possesses health hazards to the workers and the community at large. However, they take a longer time to affect the people and may be hard to prove. Nevertheless, most people who live around oil refineries are familiar with the air and water pollution from such plants (Eyayo, 2014). Correspondingly, mining, burning and refining the oil pose a serious health challenge. Some of the common ailments associated with oil refinery include blurred vision, lung and throat cancer, asthma, pneumonia, bronchitis, and birth defects. Therefore, the oil refineries should adopt the best standards such as providing employees with protective gear to avoid the health hazards accompanied with the industry (Eyayo, 2014).
Results
An investigation in an oil refinery plant exposes one to the first-hand operations that take a plane, the challenges encountered, and any other outstanding factors. Various mechanical and electrical equipment are used at these sites due to the complexity of the approach as well as the safety concerns (Devold, 2006). The first stages of mining involve drilling into the ground to obtain the resource. Oil exists thousands of feet below the ground, thus making the process labor intensive, capital intensive, and complex. The drilling company also has to take into account various factors before commencing the activity such as the stability of the soil below the surface (Devold, 2006). Unstable grounds can cause a major crisis since the structure may fail at any point, thus, resulting in injury to the workers as well as the loss of expensive equipment. As such, civil and structural engineers are involved in the study of the underlying ground to determine the compressive strength of the soil below the surface and the need for reinforcing the soil. There are also safety clamps and other safety equipment that ensure that all processes are running properly. The plants also have a specialized control system for the detection of any fault (Fang, & Duan, 2014).
There are also regular maintenance and servicing operations done to the pumps, turbines, oil separation units, gas separators, and oil desalting. The constant monitoring of such equipment ensures that no machinery breaks down during production, thus slowing down the process or even causing a major crisis (Fang, & Duan, 2014). Maintenance is also essential in oil refinery since the majority of the equipment are exposed to the corrosive material. Crude oil contains various components that can corrode the equipment, and they should be properly and consistently washed with time to ensure effective operation (Steiniger, 1963). For instance, the gas separators represent a condensate knockout for the clean-up hydrocarbons, condensed moisture, solids and other admixtures. Correspondingly, water is dispensed in oil and pumped out in a water-in-oil emulsion (Steiniger, 1963). Their generation and stabilization are dispensed by mechanical impurities (limestone, metal particles, clay, and sand) and fostered by oil natural emulsifying agent (naphythenes, gums, and asphaltenes). Typically, water is reactive to some metals such as calcium, magnesium, and sodium and other material such as hydrocarbons and sulfates, which contains impurities (ENCE, n.d). The presence of such substance and mechanical impurities in oil has a negative influence of the equipment needed for operations. For instance, salt deposits on pipes, heat exchange pipes, and the furnace require constant cleaning else they can cause corrosion (ENCE).
Most of the oil refineries have their power plant that supplies the energy needed for their operations. The reliance on the national electricity grid can be quite expensive given the wide array of activities that consume a lot of energy. The extensive advancement in the energy sector is trivial for the increase of the volume of mined and processes fuel at a lower cost (ENCE). The energy production centers aim at promoting energy saving for the firm while still improving the ecological condition as well as environmental protection, which is part of the global concern. The facilities emphasize on safety, and all the employees are apprised of the protocols and exit pans in the case of an incidence. This acts as a precautionary measure, although anything can happen, and important to maintain vigilance (ENCE).
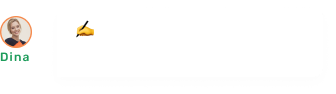
Discussion
The application of industrial separation process through distillation chamber is energy intensive, thus translating to the overall cost of the project. There have been growing concerns over the practicability and benefits of distillation of the approach in oil refineries considering the numerous technological advancements in other fields. Industrial distillation in oil refineries has been applied for more than a decade through the application of liquid and condensable gas separation (Realff & Wang, 2017). The application of multistage distillation has been the workhorse process based on the difference in the boiling points of different materials to be separated. The energy consumption of the oil refineries involves distilling the crude oil into different fractions and the subsequent separation of catalytically and thermally cracked components in the various fractions. Correspondingly, many of the bulk organic compounds in chemical engineering involve distillation in their production, thus, further extending the utilization of energy and the subsequent release of carbon dioxide (Realff & Wang, 2017). The fight against industrial and domestic pollution is more stringent than ever due to the evident impacts of pollution around the globe. There have been cases of melting polar ice, unpredictable weather conditions, drying of rivers, lakes and other water bodies, and increasing temperatures around the globe. As such, it is imperative to search for an alternative approach that is efficient. This is an important aspect of implementing the third principle of green engineering (Realff & Wang, 2017).
Here are different approaches that have been proposed by scholars that can be implemented to replace distillation or make it more efficient. One of such strategies is through integrating the process reactions with the separation to avoid the generation of mixtures that have to be separated (Realff & Wang, 2017). For instance, methanol and acetic acid produce water and methyl acetate. This reaction is equilibrium limited and results in the production of a mixture that has various binary azeotropes between components (Realff & Wang, 2017). The original approach involves the use of a decanter, one liquid extractor, and eight distillation chambers. However, this complex method was replaced with a single unit that integrates the reaction into the separation process. The major assumption of this method is that in case water leaves the liquid phase and methyl acetate leaves the liquid state, then an equilibrium conversion is avoided, and the feeds can be entirely converted to products. This system costs about 1/5th the capital and energy costs of the traditional method (Realff & Wang, 2017).
The other aspect that can be considered is how to make the distillation process more efficient. The part that consumes the most energy in the distillation chamber is the reboiler whereby heat is utilized to create the vapor stream up through the column. The use of this complex system creates the desirable composition gradient in the column, with the lower boiling point component at the condenser and the higher boiling component more concentrated at the reboiler (Realff & Wang, 2017). Under this system, the heat of condensation is released at a lower temperature than the of vaporization is absorbed. Vapor compression can be applied to fill the energy gap that causes the intense energy uses by the reboiler. Vapor compression increases the vapor temperature and reuses the heat matched at the reboiler. This will improve the energy efficiency of the distillation chamber, thus affecting the overall costs. Additionally, this will lead separation processes for dilute products that would not be energy efficient otherwise (Realff & Wang, 2017).
The other strategy that has been suggested by Realff & Wang (2017) is developing an alternative separation technique that can replace distillation. One of the shortcomings of the distillation approach is that it does not utilize the specific differences in the molecular size or the other physicochemical properties such as the affinity solid adsorbents or solvents, thus providing other selective approaches that can potentially use less energy (Realff & Wang, 2017). However, many of such approaches face one crucial challenge: they lack the capacity to produce the required items in the scale. As such, they cannot supply the required flow rates for the gasoline and other petroleum products (Lee, Arnot, & Mattia, 2011). Furthermore, distillation has been used for centuries and relies on the many years of experience in operations. These factors have hampered the attempts to introduce an alternative approach with the other energy efficient technologies. However, there is one technology that has broken the hold of distillation and can be applied for large scale (Lee et al., 2011). Reverse osmosis membrane is a separation technique for water desalination and uses mechanical pressure to overcome the osmotic pressure that is exerted by the salt solution and thereby push the water through a selective skin (Lee et al., 2011). The membranes that can be applied for oil refinery purposes are large and have a large surface area that allowing the production in scale (Garud, et al., 2011). The use of such technology will make chemical engineering field competitive from an energy perspective and regarding the overall costs incurred (Garud, et al., 2011). The application of the green engineering demands the application of energy efficient approaches through capital-intensive technologies.
Conclusion
In conclusion, the growing demand for energy efficient methods in refining oil has prompted researchers to conduct further studies into the field. The transport industry demands about 50% from every unit of refined oil, but only 30-40% can be raised, and thus the deficit is attained through the application of complex processes to convert petroleum fractions into gasoline. This is typically done through cracking the heavy residual products, reforming the products and isomerization. There are different stages in refining oil: separation, conversion, and treating. In the separation stage, the molecules are separated by atmospheric distillation at the normal atmospheric pressure. The oil is heated to a temperature of 350-400°C at the bottom of a 60-meter distillation chamber, causing the oil to vaporize. The conversion stage cracks the heavy hydrocarbons left at the separation stages done at 500°C and is referred as catalytic cracking since it applies a catalyst to speed up the chemical reaction. The last treating stage involves the removal of molecules and substances that are corrosive and that cause increased air pollution, such as sulfur.
There different approaches that can be applied for detecting the various faults that may occur. The timeliness, effectiveness, and accuracy of the fault detection and diagnosis will increase safety, product quality, and reduce the downtime and costs of operations. Most refineries rely on skills and experience of the staff in the detection of such faults. However, a fault detection analysis such as wavelet analysis can be applied to reveal faults in the industry at different levels. Correspondingly, there are also health hazards that exist in the industry such as blurred vision, lung and throat cancer, and asthma. Therefore, the oil refineries should adopt the best standards such as providing employees with protective gear to avoid the health hazards accompanied with the industry. Additionally, it is imperative to introduce alternative refining strategies to replace distillation method such as the reverse osmosis membrane. The use of such technology will make chemical engineering field competitive from an energy perspective and regarding the overall costs incurred.
- AFPM. (2017). The Refining Process. Retrieved from https://www.afpm.org/the-refinery-process/
- Devold, H. (2006). Oil and gas production handbook an introduction to oil and gas production, transport, refining and petrochemical industry. Retrieved from https://library.e.abb.com/public/34d5b70e18f7d6c8c1257be500438ac3/Oil%20and%20gas%20production%20handbook%20ed3x0_web.pdf
- ENCE (n.d). Equipment for Oil and Gas Production. Retrieved from http://www.ence.ch/eng/equipment_ngd.php#drilling-equipment
- Eyayo, F. (2014). Evaluation of Occupational Health Hazards among Oil Industry Workers: A Case Study of Refinery Workers. Journal of Environmental Science, Toxicology and Food Technology, 8(12), 22-53.
- Fang, H., and Duan, M. (2014). Offshore Operation Facilities: Equipment and Procedures. Amsterdam: Gulf Professional Publishing.
- Freyermuth, B. and Isermann, R. (2014). Fault Detection, Supervision and Safety for Technical Processes 1991: Selected Papers from the IFAC/IMACS Symposium, Baden-Baden, Germany, 10–13 September 1991. Oxford: Pergance Press Ltd.
- Garud R. M., Kore S. V., Kore V. S., Kulkarni G. S. (2011). A Short Review on Process and Applications of Reverse Osmosis. Universal Journal of Environmental Research and Technology, 1(3), 233-238.
- Groysman, A. (2016). Corrosion Problems and Solutions in Oil Refining and Petrochemical Industry. Tel Aviv: Springer.
- Koodali, R., Golisz, S. and Armstrong, D. (2017). Oil and Petroleum. American Chemical Society. Retrieved from https://www.acs.org/content/acs/en/careers/college-to-career/chemistry-careers/oil-petroleum.html
- Lee, K. P., Arnot, T. C., & Mattia, D. (2011). A review of reverse osmosis membrane materials for desalination—Development to date and future potential. Journal of Membrane Science, 370(2), 1-22.
- Marti, L., Sanchez-Pi, N., Molina, J. M. and Garcia, A. C. B. (2015). Anomaly Detection Based on Sensor Data in Petroleum Industry Applications. Sensors, 15, 2774-2797.
- Petroleum UK. (2017). Fuel from Crude Oil. Retrieved from http://www.petroleum.co.uk/refining
- Planete Energies. (2015). Feature Report: About Refining. Retrieved from http://www.planete-energies.com/en/medias/close/three-stages-refining
- Realff, M. J. and Wang, D. (2017). Green Engineering Principle #3 Design for Separation. American Chemical Society. Retrieved from https://www.acs.org/content/acs/en/greenchemistry/what-is-green-chemistry/principles/12-principles-of-green-engineering/green-engineering-principle-3.html
- Steiniger, E. L. (1963). Materials Requirements for Oil and Gas Exploration, ‘ Drilling and Production 1962. The National Petroleum Council. Retrieved from http://www.npc.org/reports/1963-Materials_Requirements-Oil_and_Gas_Exploration-Drilling-Production.pdf
- World Crude Oil Refineries (n.d). Oil Refinery Processes. Retrieved from http://uma.ac.ir/files/site1/m_ghorbanpour_6ffe535/refinery_3.pdf